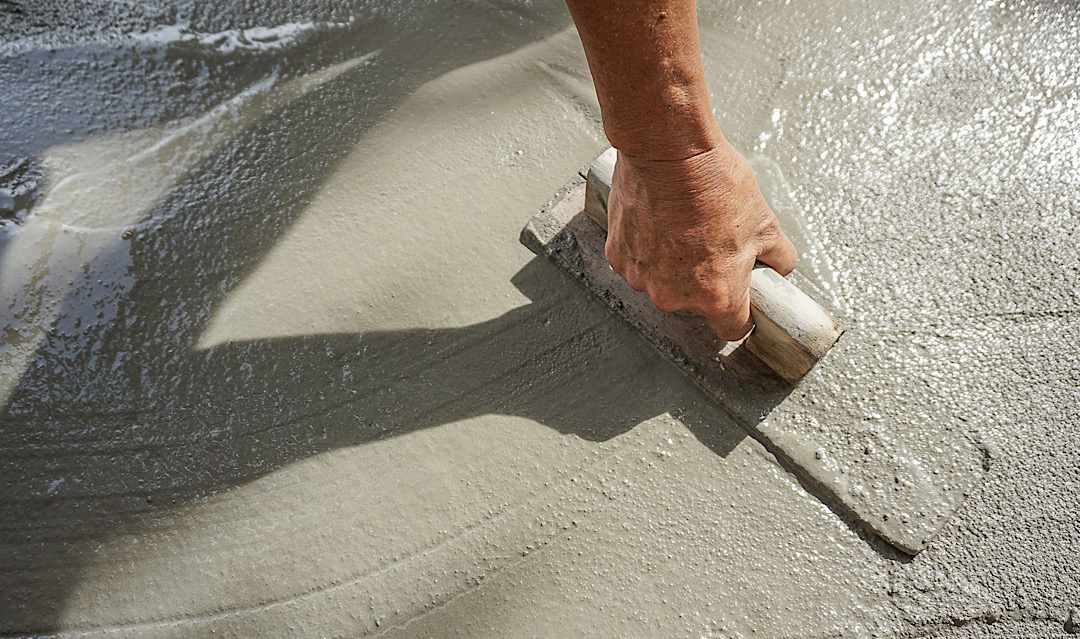
Concrete is a durable and versatile building material, but its longevity can be compromised by exposure to water, chemicals, and temperature fluctuations. Sealing joints and surfaces in concrete structures is crucial for protecting them from these elements and extending their lifespan. This article outlines the best practices for sealing joints and surfaces in concrete structures to ensure long-term durability and performance.
Importance of Sealing Concrete Structures
Sealing concrete structures offers several significant benefits:
Prevents Water Infiltration: Sealing prevents water from penetrating concrete, which can cause cracks, spalling, and other forms of deterioration.
Protects Against Chemicals: Sealed surfaces are resistant to harmful chemicals and deicing salts that can degrade concrete over time.
Reduces Freeze-Thaw Damage: Sealing minimizes the impact of freeze-thaw cycles, reducing the risk of surface scaling and cracking.
Enhances Durability: Sealed concrete surfaces are more resistant to abrasion and wear, extending the structure’s lifespan.
Improves Aesthetic Appeal: Sealing can enhance the appearance of concrete by providing a uniform finish and protecting against stains and discoloration.
Best Practices for Sealing Joints in Concrete Structures
Sealing joints in concrete is essential to prevent water ingress and accommodate movements caused by thermal expansion, contraction, and load stress. Here are the best practices for effective joint sealing:
Choosing the Right Sealant
Selecting the appropriate sealant is critical for joint sealing. The choice depends on the type of joint, expected movements, and environmental conditions.
Silicone Sealants: Ideal for exterior joints due to their flexibility and resistance to UV radiation and weathering.
Polyurethane Sealants: Suitable for both horizontal and vertical joints, offering good adhesion, flexibility, and durability.
Epoxy Sealants: Best for joints requiring high strength and chemical resistance, typically used in industrial settings.
Acrylic Sealants: Used for less critical joints, offering good adhesion and ease of application but less flexibility.
Preparing the Joint
Proper joint preparation ensures optimal adhesion and performance of the sealant.
Cleaning: Remove all debris, dust, oil, and previous sealant residues from the joint. Use a wire brush, compressed air, or a vacuum to clean the joint thoroughly.
Priming: Apply a primer if recommended by the sealant manufacturer to enhance adhesion, especially on porous surfaces.
Backer Rod Installation: Insert a backer rod into the joint to control the depth of the sealant and create a backstop. This helps achieve the correct sealant profile and ensures flexibility.
Applying the Sealant
Correct application techniques are crucial for a durable and effective seal.
Temperature Considerations: Apply the sealant when the concrete surface and ambient temperatures are within the manufacturer’s recommended range to ensure proper curing.
Tooling the Sealant: Smooth the sealant using a tool or spatula to ensure it adheres well to the joint sides and creates a concave shape. This helps the sealant stretch and compress effectively.
Curing Time: Allow the sealant to cure fully before exposing it to traffic or environmental stresses. Follow the manufacturer’s instructions for curing times.
Best Practices for Sealing Concrete Surfaces
Surface sealing is essential for protecting concrete structures from environmental damage and wear. Here are the best practices for effective surface sealing:
Selecting the Right Sealer
Different sealers offer various levels of protection and finishes. Choose the right sealer based on the specific requirements of your concrete structure.
Penetrating Sealers: These sealers penetrate the concrete and form a chemical barrier that repels water and contaminants. They are ideal for exterior surfaces and provide long-lasting protection without altering the appearance of the concrete.
Acrylic Sealers: These form a protective film on the surface, enhancing the appearance with a glossy or matte finish. They are suitable for interior and exterior surfaces but may require reapplication over time.
Epoxy Sealers: Provide a hard, durable finish with excellent chemical resistance. They are commonly used in industrial and commercial settings where heavy wear and chemical exposure are concerns.
Polyurethane Sealers: Offer a strong, flexible protective layer that resists abrasion and chemicals. They are suitable for high-traffic areas and can be used both indoors and outdoors.
Surface Preparation
Proper preparation of the concrete surface is crucial for the sealer to bond effectively and provide long-lasting protection.
Cleaning: Thoroughly clean the surface to remove dirt, grease, oil, and previous coatings. Use pressure washing for exterior surfaces and appropriate cleaners for interior floors.
Repairing Cracks and Defects: Fill any cracks and repair damaged areas before applying the sealer to ensure a smooth, uniform finish.
Drying: Ensure the concrete is completely dry before applying the sealer. Moisture can prevent the sealer from adhering properly and cause it to peel or blister.
Application Techniques
Proper application techniques are essential for achieving a durable, protective seal.
Temperature and Weather Conditions: Apply the sealer when the temperature is within the recommended range, and avoid application in direct sunlight or extreme weather conditions.
Application Method: Use a brush, roller, or sprayer to apply the sealer evenly across the surface. Follow the manufacturer’s recommendations for application thickness and number of coats.
Curing Time: Allow sufficient curing time before exposing the sealed surface to traffic or environmental conditions. Follow the manufacturer’s instructions for drying and curing times to ensure optimal performance.
Maintenance of Sealed Concrete Surfaces
Regular maintenance is essential to prolong the life of sealed concrete surfaces and ensure they continue to provide effective protection.
Regular Cleaning: Clean sealed surfaces regularly to remove dirt, debris, and contaminants that can wear down the sealer.
Inspect for Damage: Periodically inspect sealed surfaces for signs of wear, damage, or peeling. Address any issues promptly to prevent further deterioration.
Reapplication: Depending on the type of sealer and the level of wear, reapply the sealer as needed to maintain its protective properties. Follow the manufacturer’s guidelines for reapplication intervals.
Sealing joints and surfaces in concrete structures is a crucial step in ensuring their longevity and performance. By following best practices for selecting and applying sealants and sealers, and maintaining sealed surfaces regularly, you can protect your concrete structures from water infiltration, chemical damage, and environmental wear. Implementing these practices will help extend the lifespan of your concrete structures, reduce maintenance costs, and enhance their overall durability and appearance.